Manufacturing has evolved immensely over time and CNC machining is the prime example of this advancement. CNC, which stands for computer numerical control, is a special technique where a computer is utilized to manage machines for activities like cutting, drilling, milling, and shaping materials.
Unlike manual machining, CNC turned Components speeds up production, enhances accuracy, and makes the manufacturing operation more efficient and cost-effective. These advantages make it a critical instrument in today’s industries.
In this blog, we’ll look at the top 7 reasons for utilizing CNC machining that highlight why it’s become necessary for precision engineering.
Table of Contents
How Are Precision-Turned Components Made?
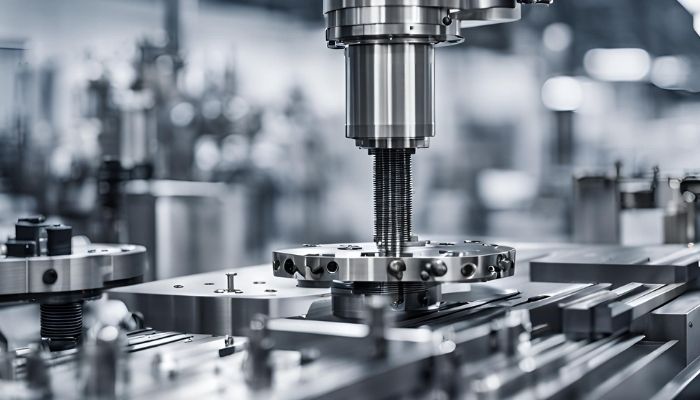
CNC turned components are made by rotating a cylindrical piece on a CNC lathe or machine. Cutting tools, end mills, and drills shape the part to the exact size and form needed. This method assures that the finished piece is highly precise and meets the performance benchmarks needed for demanding commercial uses.
Reasons To Choose CNC Turned Components In Your Power Systems
Let’s unfold several reasons that encourage individuals to use CNC precision turning components to develop a wide range of complex parts like bearings, linkages, and power transmission components that are utilized in the automotive production and other commercial industries.
1. High Efficiency
One of the major benefits of CNC precision-turned components is their superior accuracy. CNC machines are programmed with special specifications such as tight tolerances that enhance the overall work. The usage of such components reduces the risk of human error and makes the task easy.
2. Reduced Waste And Cost Efficiency
The traditional machining methods frequently result in high material waste. On the other hand, CNC turned part are highly efficient resulting in reduced material waste compared to traditional machining methods.
Additionally, the automation of CNC machines lowers labor expenses and production time. Although the early setup of CNC machining might involve more increased costs but the long-term savings through decreased waste and efficient production can set off these initial expenses that make it a cost-effective option for greater results.
3. Dimensional Accuracy And Reduced Human Error
CNC machining can consistently meet exact measurements no matter how many components are produced which ensures accuracy throughout the entire manufacturing cycle. This technology allows for reducing mistakes and cutting costs by using materials more efficiently and minimizing waste. This can lower the cost per unit of CNC-turned parts. It also makes checking and approving parts easier.
4. High Repeatability
CNC Turned components are recognized for their capability to produce similar parts repeatedly which is essential for making the same elements in consumer products. CNC machines can consistently manufacture the same parts over long periods and through endless production runs which makes them ideal for large-scale production where each piece needs to meet exact specifications every time.
5. User Friendly And Safe
The precision and consistency of CNC-machined parts make them safer and easier to use. This reduces the chances of receiving defective components, mechanical failures, and issues that eventually save you and your users money on repairs and maintenance over time.
6. Capability Of Manufacturing High-Quality Parts
Investing in precision turned parts permits you to have more power over the materials and dimensions of your components. You can choose from diverse materials such as steel, titanium, aluminum, chromium, or even additional types of thermoplastics and acrylics. This can be done while maintaining top quality, precision, and timely production.
7. Rapid Prototyping
In the fast-moving domain of product development, CNC machining is excellent for rapid prototyping as it allows designers and engineers to quickly modify designs and test ideas before starting large-scale production. This speeds up the innovation procedure and shrinks the time it takes to bring a product to market.
8. Creativity Aspect
With its multi-dimensional capabilities, CNC machining can create complicated shapes that would be difficult or impossible with traditional machining methods. This leads to the expansion of design possibilities and permits engineers to explore new levels of creativity.
Conclusion
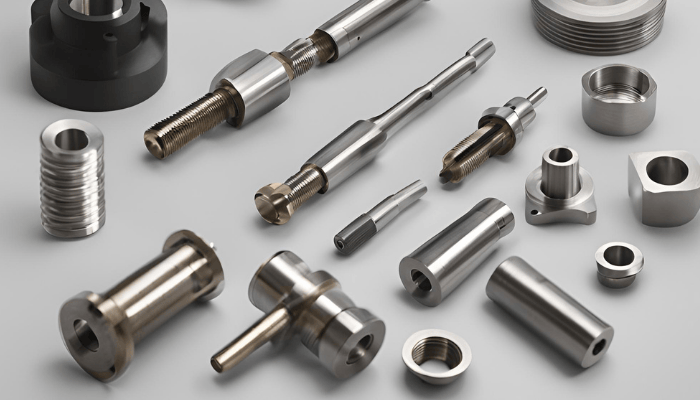
CNC turning components is a critical element of modern manufacturing. In this blog, we’ve understood how CNC turned components work and their advantages. With constant improvements and the potential for more automation, CNC turned parts will remain essential in manufacturing leading to innovations across different enterprises.