The need for components with exceptional conductivity, robustness, and longevity is greater than ever in the field of contemporary electrical engineering. In order to meet these exacting standards, manufacturers are using precision machining techniques as devices get smaller, stronger, and more dependable. Using copper precision turned parts for electrical use is one noteworthy solution.
These parts, which have remarkable electrical and thermal qualities, are the foundation of innumerable applications, ranging from fixtures and heat sinks to connectors and terminals. Global Precision Pvt Ltd, a prominent supplier of high-precision machining services, specializes in producing superior CNC-turned components and parts that are built to last in the most requested electrical environments.
Why Copper?
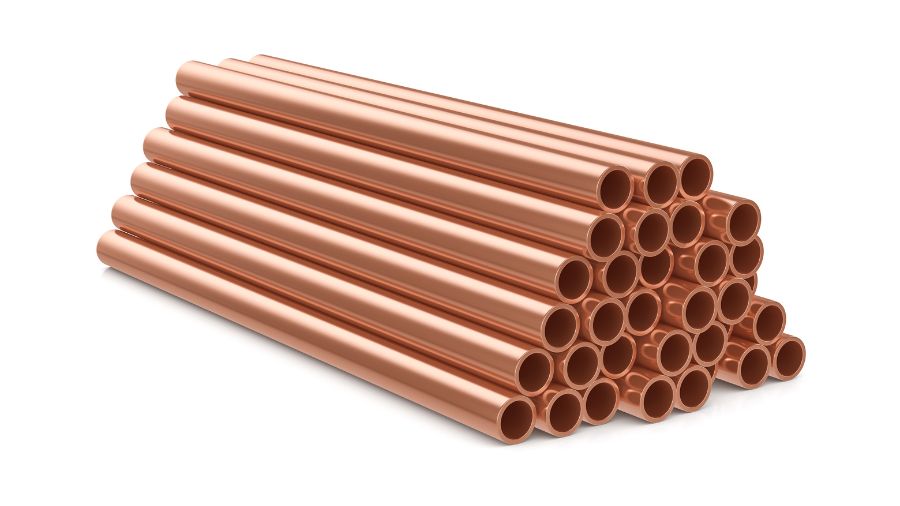
Copper is the preferred material for electrical applications due to its special combination of physical and chemical characteristics –
- Electrical Conductivity – Among all commercially available metals, copper has one of the highest conductivities, which guarantees effective energy transfer and little power loss.
- Thermal Conductivity – Superior heat dissipation keeps systems stable and safe by preventing overheating in high-current applications.
- Corrosion Resistance – Copper is shielded from deterioration by a naturally occurring oxide layer, prolonging component life even in challenging conditions.
- Mechanical Ductility – Complex geometries and thin profiles are made possible by copper’s ability to be precisely machined to tight tolerances without breaking or cracking.
- Recyclability – Copper’s completely recyclable nature promotes environmentally friendly production methods.
Designers can create electrical systems that are lighter, cooler, and more effective by utilizing these benefits.
The CNC Turning Process
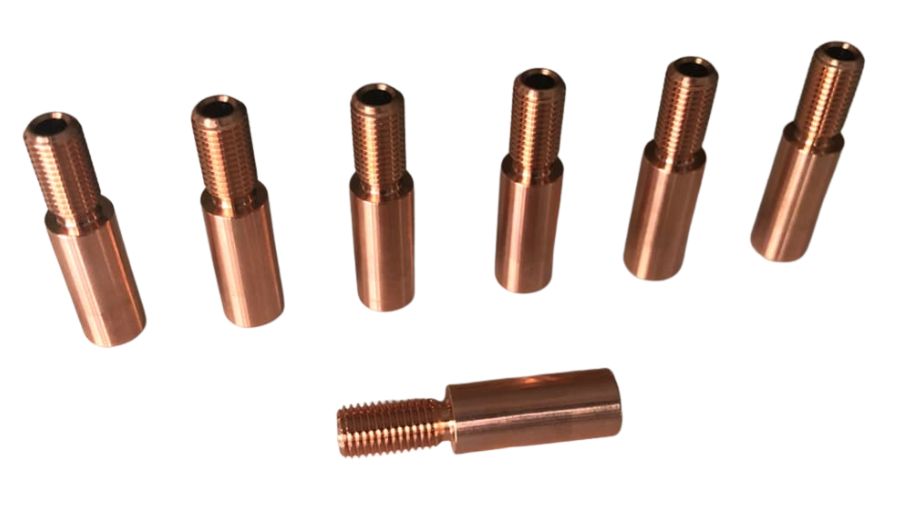
Advanced CNC turning technologies are essential to the production of copper precision turned parts for electrical use. In CNC (Computer Numerical Control) turning, a copper workpiece is rotated while the material is removed by precision cutting tools to produce the required dimensions and shape. Among the main advantages of this process are –
- High Precision – In electrical assemblies, where even small misalignments can cause performance problems, tolerances as small as ±0.005 mm guarantee consistent fit and function.
- Repeatability – Automated toolpath coding ensures consistency throughout lengthy production runs, lowering scrap rates and guaranteeing that each batch satisfies requirements.
- Surface Finish – Smooth surface textures enhance the mating of conductive surfaces and reduce contact resistance.
- Flexibility – Agile manufacturing workflows are supported by quick tool changes and multi-axis capabilities, which enable quick transitions between various part designs.
- Cost Efficiency – Faster cycle times made possible by high spindle speeds and optimized feed rates reduce costs per piece without sacrificing quality.
Key Electrical Applications
Copper Precision Turned Parts for Electrical Use are essential components in many different fields and applications –
- Terminals and Connectors – In electrical distribution and signal transmission systems, precision-turned pins, sockets, and crimp fittings offer dependable, low-resistance connections.
- Parts of Switchgear – Copper-made arcing contacts, contact fingers, and busbars guarantee steady, high-current switching with little wear.
- Parts for Transformers – Transformer effectiveness and thermal management are maximized by machining lead wires, winding separation devices, and cooling inserts.
- Generator and Motor Components – Exact tolerances are necessary for shaft collars, slip ring assemblies, and segments of commutators in order to preserve performance and lower electrical noise.
- Thermal Interfaces and Heat Sinks – In telecom equipment, LED lighting, and power electronics, turned copper fins and mounting fixtures improve heat dissipation.
- Microwave and Radio Frequencies – For minimal signal loss, precision-turned waveguide sections and antenna fittings require smooth surfaces and stringent dimensional control.
Engineers can create reliable, high-performing final products by incorporating Copper Precision Turned Parts for Electrical Use into these systems.
The Advantage Of CNC Turned Components & Parts
For manufacturers of electrical equipment, selecting premium CNC turned components & parts has several advantages –
- Design Freedom – Design freedom simplifies assembly and boosts performance by enabling the production of intricate geometries, internal features, and undercuts in a single setup.
- Material Efficiency – By minimizing waste, near-net-shape turning lowers material costs and its environmental impact.
- Scalability – CNC turning allows for quick scaling without compromising quality, whether you require small prototype batches or large-scale production.
- The integration of Secondary Operations – Lead times can be reduced by smoothly integrating extra operations like drilling, threading, or knurling into a single machine cycle.
- Improved Reliability – Consistent output is ensured by strict process control and real-time monitoring, which lowers field failures and warranty claims.
Shorter time-to-market, lower total cost of ownership, and better end-product performance are all concrete benefits that result from these strengths.
Benefits Of Connecting With A Manufacturer
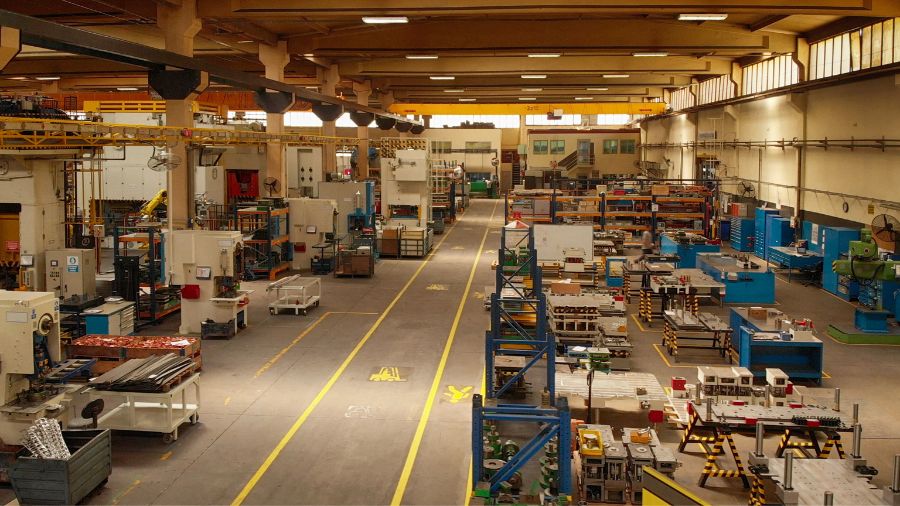
This reputable manufacturer, a leading supplier of Copper Precision Turned Parts for Electrical Use, blends state-of-the-art technology with extensive industry knowledge –
- Modern Equipment – We can handle even the most intricate copper components with unparalleled precision thanks to multi-axis CNC lathes with live tooling and robotic automation.
- Quality Management Certification – Our quality systems guarantee that each batch is subjected to stringent inspection and traceability, in accordance with ISO 9001:2015 and IATF 16949:2016 automotive standards.
- Material Mastery – To customize mechanical and electrical properties to your application requirements, skilled metallurgists advise on alloy selection and heat treatments.
- Collaborative Engineering – We optimize cost and performance while speeding up product development with our design-for-manufacturability (DFM) services and rapid prototyping.
- Global Supply Chain – We consistently deliver to clients in Asia, Europe, and the Americas on schedule thanks to an effective logistics network.
- Sustainability Focus – We recycle scrap copper, use less energy, and produce less waste in accordance with green manufacturing principles.
You get a committed partner who is dedicated to quality and innovation when you choose Global Precision Pvt Ltd for your CNC Turned Components & Parts.
The need for Copper Precision Turned Parts for Electrical Use will only grow as electrical applications continue to change due to developments like electric vehicles (EVs), renewable energy sources, and 5G infrastructure.
Advanced surface treatments, hybrid machining additive methods, and copper alloy innovations hold the promise of releasing even more performance potential. With the help of a forward-thinking partner like Global Precision Pvt Ltd, manufacturers are able to deliver the next generation of electrical products and stay ahead of the curve.
Conclusion
The modern electrical industry depends on the precise machining of copper components. Copper Precision Turned Parts for Electrical Use provide the performance, dependability, and efficiency that contemporary systems require in everything from heat sinks and RF fittings to high-current connectors and switchgear components.
Businesses can save costs, improve quality, and speed up product development by selecting CNC Turned Components & Parts from a reputable component manufacturing company like Global Precision Pvt Ltd. To find out how we can collaborate with you on your upcoming electrical project and use precision engineering to spur innovation, get in touch with our team right now.