With the intense competition in the industrial sector, the demand for Precision Machined Components has greatly increased in today’s time. In aerospace parts or medical devices, the components made have to keep to very close tolerances and standards, whether it be the fit, finish, or performance.
Be it research into Precision Components Manufacturers or looking for a trusted Precision Machined Components Manufacturer like Global Precision Pvt Ltd, knowledge about the making of these parts reveals why expertise and process control are quite so important in this world.
This guide gives you a step-by-step view of the world of precision parts from conceptual design all the way to the final inspection.
Table of Contents
Know The Process Of Making Precision Machined Components
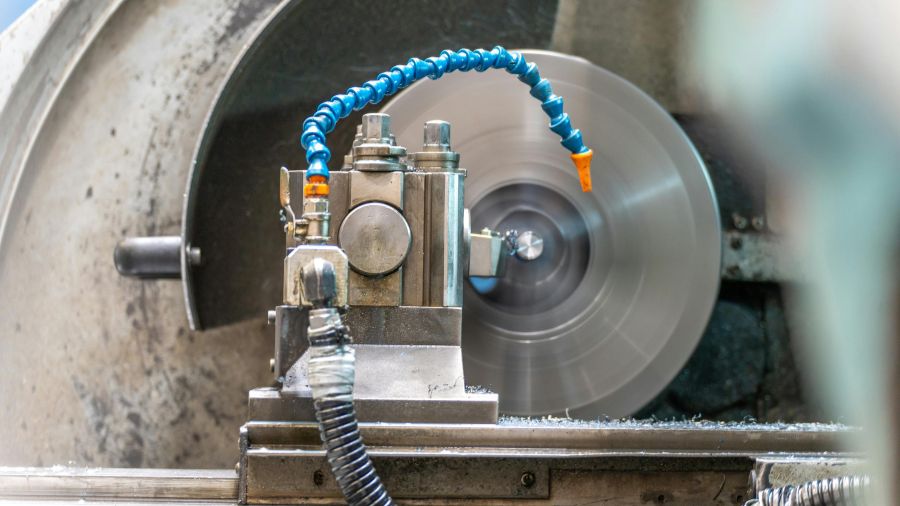
1. Concept & Design
An idea is where it starts – every Precision Machined Components. Nothing is released until dimensions, tolerances, materials, and functional needs—engineering and design combined efforts that transpire toward a detailed CAD model from customer requirement variables.
- Requirement Gathering – Customers specify operating conditions, load requirements, and environmental factors.
- CAD Modeling – Modeling in software such as SolidWorks or Autodesk Inventor generates a 3D representation.
- FEA & Simulation – The finite-element analysis tests a model’s ability to sustain stresses and strains in real-world conditions before it can be adjusted to specifications.
Among the most important decisions you can make in this early stage is selecting a good Precision Parts Manufacturer, one with respectable design review capabilities. It will save you a lot of time and cost down the road. Global Precision Pvt Ltd usually involves partnering with clients from the idea stage for manufacturing feasibility and cost efficiencies.
2. Material Selection
Material selection impacts Precision Machined Component performance and its durability. Common materials are as follows –
- Metals – Lightweight, good strength, aluminum alloys; corrosion resistant, stainless steel; highly strength to weight ratio, titanium; good wear resistance, tool steels.
- Plastics – Engineering plastics used include PEEK, Delrin, etc., which are for applications that consider low friction with lightweight.
- Composites – Carbon-fiber-reinforced polymers-high strength yet low weight.
Factors influencing selection –
- Mechanical Properties – Such as tensile strength, hardness, and fatigue factors.
- Thermal Properties – This must refer to expansion rates and conductivity.
- Chemical Compatibility – With corrosive or worn or exposed chemicals.
- Cost & Availability – That is compromising between performance expectations with budgets.
Precision Components Manufacturers having a textured depth of material knowledge like Global Precision Pvt Ltd can recommend materials that conform to performance and cost targets.
3. Programming & Toolpath Generation
After fixing the design and the material, we import the CAD model into CAM (Computer-Aided Manufacturing) software, where a detailed plan for the manufacture is laid out.
- Tool Selection – This would involve end mills, drills, taps, and other specialized cutters applicable to that choice of material and geometry.
- Toolpath Strategy – Which way to rough out- that is remove bulk material quickly- and finish-tight intolerances and smooth surfaces?
- Feeds & Speeds – Calculate spindle speeds and feed rates so as to balance material removal with tool wear/part deformation.
This phase weighs heavily on any Precision Machined Components Manufacturer since any programming-related error results in scrapped parts or missed tolerances. Global Precision Pvt Ltd employs an experienced team of CAM programmers who use sophisticated software to simulate precisely every single cut path before the actual machining process starts.
4. Machine Setup
With the preparation of the CAM program, the Precision Parts Manufacturer can progress to setting up the machines –
- Fixture Design – Custom jigs and fixtures firmly hold the raw material block for repeatable accuracy.
- Machine Calibration – CNC machines (milling centers, lathes, or Swiss-type lathes) undergo frequent calibration for alignment along axes and spindle integrity.
- Tool Loading – Cutting tools get loaded into automatic tool changers, and offsets are measured accurately with presetter devices.
A good setup process is a hallmark of a top Precision Machined Components Manufacturer. At Global Precision Pvt Ltd, every fixture and machine is logged, maintained, and verified for consistency across batches before production commences.
5. Rough Machining
Roughing-the actual initial phase of physical machining is defined simply as removing excess materials at a fast pace, approximating the final shape.
- High-Rate Material Removal – Larger diameter cutters at a high feed rate.
- Coolant application – Flood or mist cooling prevents heating and, as a consequence, distortion and accelerated tool wear.
- Chip Management – Efficient evacuation of the metal chips to prevent re-cutting and damage.
Rough machining neither imparts final tolerances but rather maximizes the reduction in cycle time. The Precision Components Manufacturers employ materials strategic toolpaths, staying within the shortest time possible with machine time while ensuring that adequate stock is left for subsequent operations.
6. Semi-Finishing & Finishing
When most material is removed, one has to enter into delicate operations –
- Semi-finishing – Smaller tools refine critical profiles and start getting close to the target dimensions, leaving a slight allowance.
- Finishing – Fine end mills, ball mills, or lathes complete the part to its final dimensions–often within microns (±0.005 mm).
- Surface treatments – In addition to the above, parts may go through treatments such as honing, polishing, or bead blasting, depending on requirements, to achieve the required surface roughness (Ra).
It is at this stage that the real expertise of the manufacturer manifests itself in the precision machined components. Global Precision Pvt Ltd has specialized tooling with expert operators, consistently providing smooth finishes and accurate tolerances.
7. Quality Inspection & Metrology
Quality assurance cannot be compromised. Every batch of Precision Machined Components undergoes an intense level of inspection –
- First Article Inspection (FAI) – The very first part of the run is measured with extreme detail.
- In-Process Checks – Periodically measuring during the run assures the machine is “in spec”.
- Final Inspection – Every critical dimension is checked via Coordinate Measuring Machines (CMMs), optical comparators, and surface roughness testers.
Data from the inspections is recorded and trends analyzed; corrective action is taken on evidence of drift. Companies recognized as leading Precision Components Manufacturers integrate Statistical Process Control to ensure zero-defect levels. Global Precision Pvt Ltd provides full inspection reports and traceability documentation with each shipment.
8. Secondary Operations & Assembly
Secondary operations and Assemblies. Many precision parts undergo secondary operations beyond machining-involved manipulations. They include –
- Heat Treatment – Out-of-hardening or stress relieving, resulting in improved mechanical properties.
- Coatings & Platings – anodizing, nickel plating, or PTFE coatings build solid corrosion-resistant and lubricious surfaces.
- Assembly – A fitting together of precision parts in multi-profit parts assembly, which sometimes will need press fitting, welding, or adhesively binding the parts together.
A Complete Precision Parts Manufacturer should, however, most comprehensively include these processes, because, as one base, the time and logistical complexity will be minimized. Global Precision Pvt Ltd owns certified heat treatment and coating facilities for total control over quality and scheduling.
9. Packaging & Shipping
This is the last mile toward perfect customer satisfaction: protecting fragile components during transport.
- Custom Packaging – Foam inserts, vacuum seals, or desiccant packs prevent movement and moisture damage.
- Labeling & Documentation – Part numbers, lot codes, and handling instructions are included on every package.
- Global Logistics – Through reliable carriers and Logistics Companies In Dubai, the components are delivered on time with track-and-trace traceability.
The right Precision Machined Components Manufacturer ensures that what leaves their facility arrives at yours in perfect condition. Global Precision Pvt Ltd offers turnkey logistics solutions to streamline international deliveries.
Conclusion
The creation of Precision Machined Components is an exacting, multilayered procedure requiring expertise at every opportunity. From the initial contemplation of the design through material selection, CAM programming, machining, and extensive quality inspections, each stage plays a part in guaranteeing quality in the final product.
When working with an experienced Precision Components Manufacturer-someone trusted, like Global Precision Pvt Ltd, a genuine Precision Machined Components Manufacturer-the certainty exists that your precision parts will have exceedingly tight tolerances, high surface-quality standards, and stringent performance requirements.
From aerospace-grade components, medical device parts, and industrial tooling, process control, and experience matter upon the understanding of these nine steps. Choose your Precision Part Manufacturer well, so that your end products will continue to surpass expectations-delivered on time, on budget, and to exacting specifications.