CNC Turned Components are central to the fast-paced manufacturing world of today in various industries-from automotive and aerospace to medical devices and consumer electronics. CNC turned components offer much precision, speed, and repeatability, but ordering the wrong specifications or omitting crucial steps in the entire CNC turned components ordering process can only result in delays, quality problems, and budget overruns.
Here, we discuss and put forth some hints to avoid the common mistakes while ordering CNC turned components in order to make the entire process smooth and efficient whether you are dealing with new CNC Components Manufacturer specialists or with giants like Global Precision Pvt Ltd.
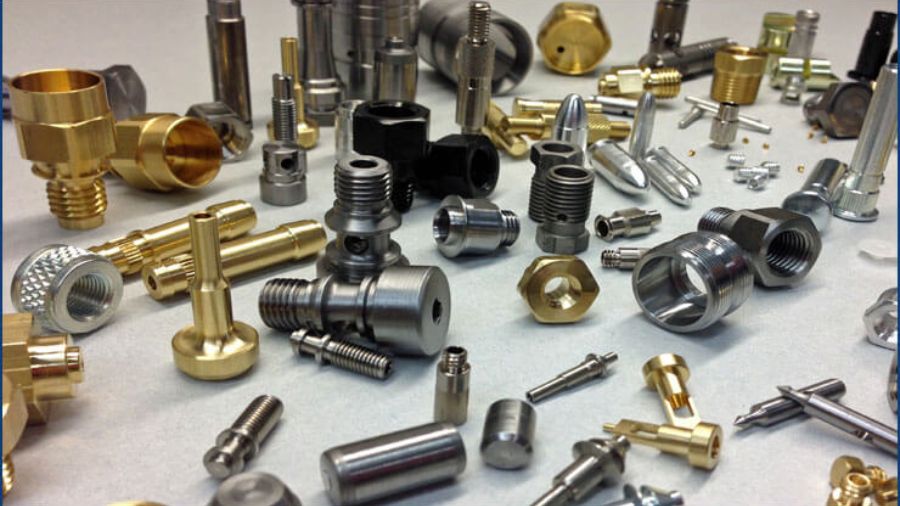
Table of Contents
List Of The Mistakes To Avoid And How To Fix Them:

1. Incomplete or Ambiguous Drawings
The Mistake – Submission of sketches or freehand drawings without dimensioning, tolerancing, or material callouts. CNC machines use their program to the letter. Any ambiguity in the drawings causes a lot of assumptions on the part of the manufacturers and, therefore, could go wrong with features, fits, or finishes.
The Solution – Use any professional CAD software to generate a good 3D model and 2D detail drawings. Clearly annotate all critical dimensions, geometric tolerances (GD&T), surface finishes, and material grades. If you’re not sure about the criticality of certain tolerances, consult your CNC Machined Components Manufacturers early in the design process.
2. Ignoring Material Selection and Its Impact
The Mistake – It is allowing cost or availability to sway a decision on the appropriation of materials. The machinability strength or corrosion resistance is forgotten in such a course of action. Being different alloys, they cut differently depending on the cuts’ speed and feed. The material used may result in excess wear on the tool, a tolerance that is missed, and parts that are rejected.
The Solution – Functional requirements have to be specified load coupled with temperature range and chemical exposure; these would then help select materials, for common applications such as aluminum alloys (6061-T6) and stainless steels (303, 316)-as they are workhorses that provide good machinability as well as corrosion resistance. Consult a trusted CNC Components Manufacturer like Global Precision Pvt Ltd responsible for such material recommendations according to the end use of your part.
3. Ignoring Tolerance Specifications
The Mistake – Every dimension is specified to ultra-tight tolerances (±0.01 mm), “just to be very safe.” Tighter tolerances always add cycle time, tooling cost, and scrap rates. Use them only when functionally necessary.
The Solution – Tolerances apply on the basis of a tolerance analysis undertaken to ascertain the dimensions that would have a functional effect on assembly, performance, and safety. Use conventional tolerances, such as ±0.1 mm, for non-critical features. Reserved for precision tolerances mating surfaces, bearing fits, or sealing interfaces. A seasoned CNC Components Manufacturer will guide you on balancing price versus precision.
4. Neglecting Surface Finish Requirements
The Mistake – Failing to specify surface finish (Ra) values, followed by discovery post-machining that a cosmetic or functional finish is needed. Surface roughness affects fatigue life, sealing surfaces, and friction. It becomes a cost and time-consuming operation requiring grinding or polishing after the original machining.
The Solution – Determine post-machining operations when specifying the finishing requirements, especially on sliding fits, or paths from liquid to gas or fluid. Data such as required Ra values should be specified in drawings (for instance, Ra 0.8 µm for bearing journals). Secondary operations, such as honing or electropolishing, should involve consultations with your CNC Machined Components Manufacturers to ensure seamless integration into the workflow.
5. Misjudging Prototype and Testing Phases
The Mistake – Immediate transition to production without a prototype or sample runs. Hidden design or tooling problems usually surface once you are handling actual parts; any adjustments made at that stage are usually very expensive.
The Solution – Start with a small pilot batch (5-10 parts) to validate fit, finish, and functionality. Use it as a trial run to refine tooling, optimize cycle times, and catch design flaws. Global Precision Pvt Ltd as a leading Precision Machined Component Manufacturer also provides very cost-effective prototype programs to work out kinks before going to large orders.
6. Failing to Communicate Special Requirements
The Mistake – Neglecting to let the producer know that there are particular specifications-calls for example, heat treatment, plating, as well as critical conditions for assembly. The failure to call out heat treatment might leave parts either too soft or too brittle, and coatings that are left out can lead to corrosion or poor adhesion.
The Solution – Post machining, prove out which operations to add (hardening, anodizing, black oxide, and so on) on the purchase order. Indicate any applicable standards or certifications (MIL-SPEC, ASTM, ISO). Verify that your CNC Components Manufacturer has the in-house or partner capabilities to perform these services and does not strip the responsibility in mid-project.
7. Ignoring Lead Times and Scheduling
The Mistake – Standard lead times are assumed as norms, completely ignoring the complexity, the type of material, or the size of the order. Unexpected delays in raw materials procurement or delays in tooling setup or machine availability can put project timelines derailed.
The Solution – Talk about realistic lead times upfront, factoring in holidays and back ordered materials, as well as shop capacity. Build buffer time for prototype validation and quality inspections. A reliable CNC Components Manufacturer would love to tie you up with Gantt-type schedules or dashboards for work in progress so that you can monitor progress and anticipate bottlenecks.
8. Overlooking Quality Assurance Processes
The Mistake – Not verifying inspection protocols and assuming all manufacturers conduct the same quality checks. Parts arriving either out of tolerance or with surface defects can cause a halt to the assembly line and damage the customer relationship.
The Solution – Ask for quality certifications issued by the manufacturer, such as ISO 9001 or AS 9100, and learn about their inspection methods. Establish inspection requirements: first-article inspection (FAI), in-process checks, and final reports. Partner with your CNC Machined Components Manufacturer to provide CMM reports, SPC, and full traceability.
9. Opting For Lowest Bid Without Due Diligence
The Mistake – Selecting a CNC Components Manufacturer based on the lowest price quote. Manufacturers that offer low costs may compromise on tooling maintenance, skilled labor, or the quality of materials, giving inconsistent results.
The Solution – Cost considerations must be balanced against proven track records, technical capabilities, and service quality. Request references, facility tours (either virtual or actual), and case studies demonstrating similar parts. Understand manufacturers like Global Precision Pvt Ltd, in some cases a little more pricey, bring in actual greater value because of reworks and on-time deliveries and first-pass yields.
10. Skipping The Feedback Process After Delivery
The Mistake – Not providing performance feedback after delivery of parts; thus leaving the manufacturer unaware of the real-world problem. There could be repetitive mistakes in subsequent orders, as there is not creating any opportunity for continuous improvement.
The Solution – Share with your CNC Machined Components Manufacturer any fitting issues, tool wear observations, or assembly difficulties. Jointly carry out a root-cause analysis on any non-conformances. Hold regular review meetings in order to discuss imminent projects, process improvements, and cost-saving initiatives.
Conclusion
Specializing in high-precision turned parts will not necessarily make ordering a painful experience. It shall avoid some pitfalls like vague drawings, bad material choices, unchecked tolerances, and many more, to make the project a successful project. Partnering with the most experienced CNC Components Manufacturers, like Global Precision Pvt. Ltd., also provides you with design capabilities, material knowledge, manufacturing expertise, and quality systems to guarantee flawless delivery of CNC Turned Components on time and within budget.
There are great ways for you to streamline all your CNC turning projects and have the precision, reliability, and performance that modern manufacturing promises-. Clear communication, realistic planning, and mutual feedback are cornerstones of a productive collaboration.
Also Read: Global Precision: Leading The Way As Precision Components Manufacturer in Noida