Efficiency, durability, and accuracy are critical in the quickly changing field of automotive engineering. Manufacturers are always looking for methods to lighten their vehicles, increase their fuel efficiency, and improve their overall performance. The use of Aluminum Turned Components for Auto Industry is one important solution that has surfaced at the forefront of this change.
From engine parts to chassis systems, these parts are perfect for a variety of automotive applications because they provide a good balance between strength and lightweight. Global Precision Pvt Ltd is a top component manufacturing company that specializes in providing premium aluminum turned parts that are suited to the exacting specifications of contemporary car manufacturing.
Table of Contents
Why Aluminum?
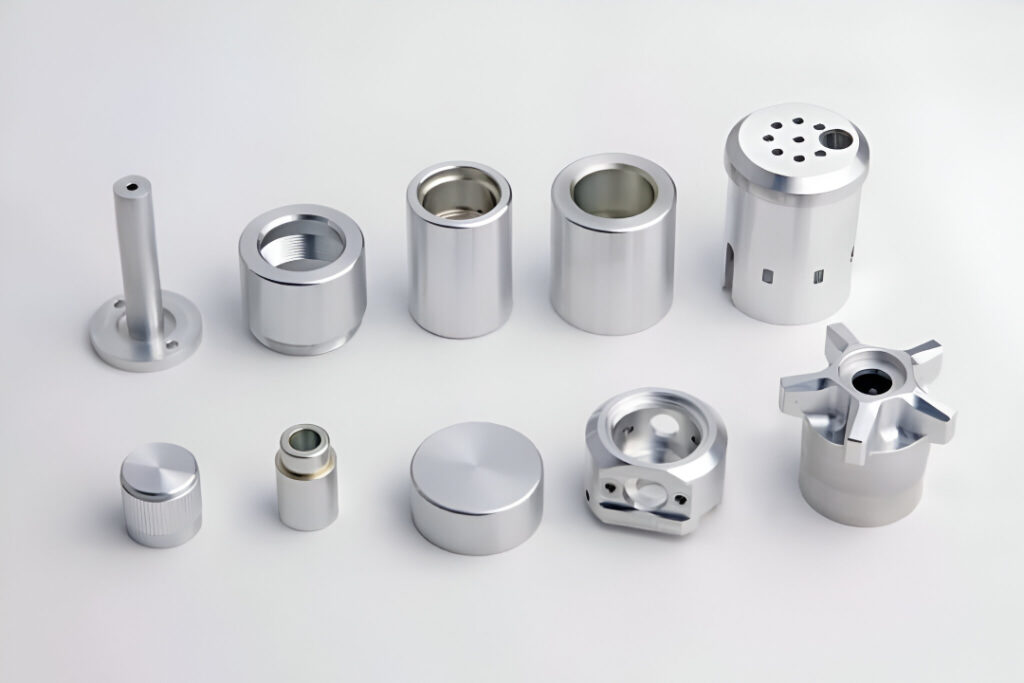
Aluminum has long been known for its remarkable qualities, which make it a material of choice for automotive parts –
- Lightweight – Because aluminum weighs around one-third less than steel, vehicles can have much lower mass, which lowers emissions and fuel consumption.
- High Strength-to-Weight Ratio – Modern aluminum alloys are strong enough to compete with steel, offering the structural integrity required for demanding applications.
- Corrosion Resistance – Naturally occurring oxide layers shield aluminum from the elements, prolonging the life of the component.
- Superior Thermal Conductivity – Perfect for heat exchange and engine components where effective heat dissipation is crucial.
The automotive industry can meet strict emissions regulations while producing vehicles with optimal performance by utilizing these properties.
The Role of Turning in Automotive Manufacturing
Using cutting tools to remove material from a rotating workpiece is known as turning. This technique is very flexible and can create intricate geometries, precise tolerances, and smooth surface finishes. The following are some major benefits of turning aluminum components –
- Precision – For parts like bushings, shafts, and valve components, achieve tolerances as tight as ±0.005 mm.
- Surface Quality – For moving parts, smooth surface finishes minimize wear and friction.
- Cost-Effectiveness – In large-scale production runs, automation and high material removal rates lower costs per unit.
- Flexibility – The capacity to swiftly adjust to modifications in design and machine a range of aluminum alloys.
Applications of Aluminum Turned Components in the Automotive Industry
The Aluminum Turned Components for Auto Industry in a variety of vehicle systems
- Engine Components – Aluminum’s lightweight and thermal characteristics improve engine adaptability and heat management in pistons, piston pins, and valve guides.
- Transmission Systems – Aluminum alloy-made gears, splines, and shafts decrease rotational mass, improving fuel economy and gearshift smoothness.
- Brake Systems – The strength and resistance to corrosion of aluminum are used by caliper pistons and master cylinder parts to provide dependable braking performance.
- Suspension and steering – Aluminum is used in control arms, bushings, and tie rod ends to reduce weight and enhance handling characteristics.
- Heat exchangers – Aluminum-made hose fittings, connectors, and fittings improve radiator and intercooler thermal management.
OEMs and Tier 1 suppliers can produce lighter, safer, and more efficient vehicles by incorporating Aluminum Turned Components for the Auto Industry.
Why Choose a Specialized Component Manufacturing Company?
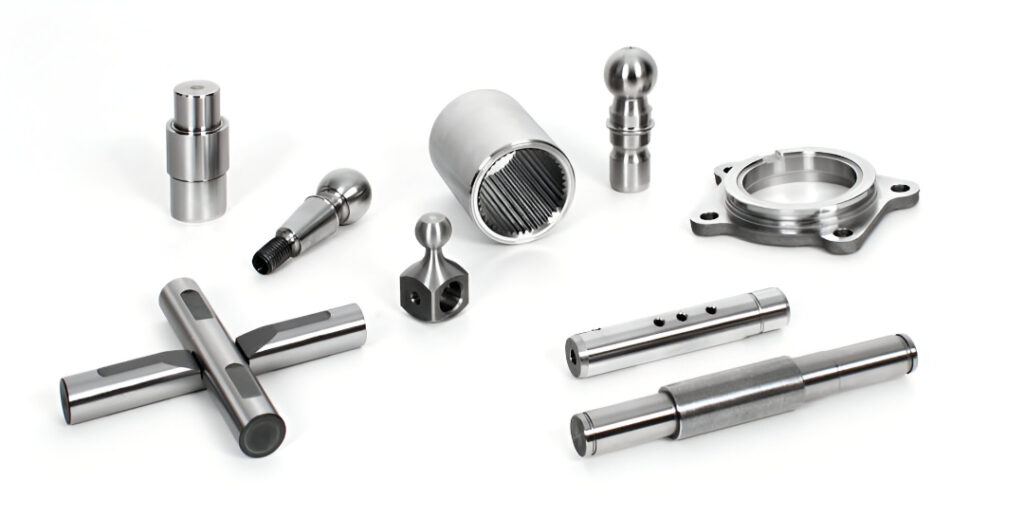
To guarantee that every part satisfies strict quality, performance, and compliance standards, choosing the correct component manufacturing company is essential. What to look for is as follows –
- Advanced CNC Turning Capabilities – Multi-axis CNC lathes with high-speed spindles and tool changers for optimal accuracy and productivity.
- Quality Assurance Protocols – Protocols for quality assurance include CMM verification, in-line inspection systems, and process control to preserve tolerances between batches.
- Material Expertise – thorough knowledge of different aluminum alloys (6061, 6082, 7075, etc.) and how to optimize mechanical properties through heat treatment.
- Regulatory Compliance – Respect for ISO 9001 certification and IATF 16949 automotive quality standards.
- Engineering Support – Value engineering, prototyping, and collaborative design for manufacturability (DFM) services to cut costs without sacrificing performance.
- Scalability – The ability to swiftly increase production levels in response to seasonal variations and market demands.
Global Precision Pvt Ltd – Your Trusted Partner
Global Precision Pvt Ltd, a leading component manufacturing company, is distinguished by its unwavering dedication to quality in aluminum-turned components for the automotive industry. What makes us the preferred partner is as follows –
- Modern Infrastructure – To guarantee high productivity and constant quality, our facility is outfitted with the newest CNC turning centers, vision examination systems, and automated material handling.
- Professional Staff – Quality inspectors, process engineers, and skilled machinists work together to produce parts that either match or surpass client requirements.
- Tailored Solutions – Our end-to-end services enable clients to expedite time-to-market, from the initial idea and prototyping to full-scale production.
- Worldwide Presence – We provide just-in-time delivery schedules to reduce inventory costs and comprehend the various market requirements of OEMs and Tier 1 suppliers worldwide.
- Practices for Sustainability – We assist clients in reaching their sustainability objectives through recycling initiatives, energy-efficient procedures, and optimized material usage.
Quality and Innovation at Every Step
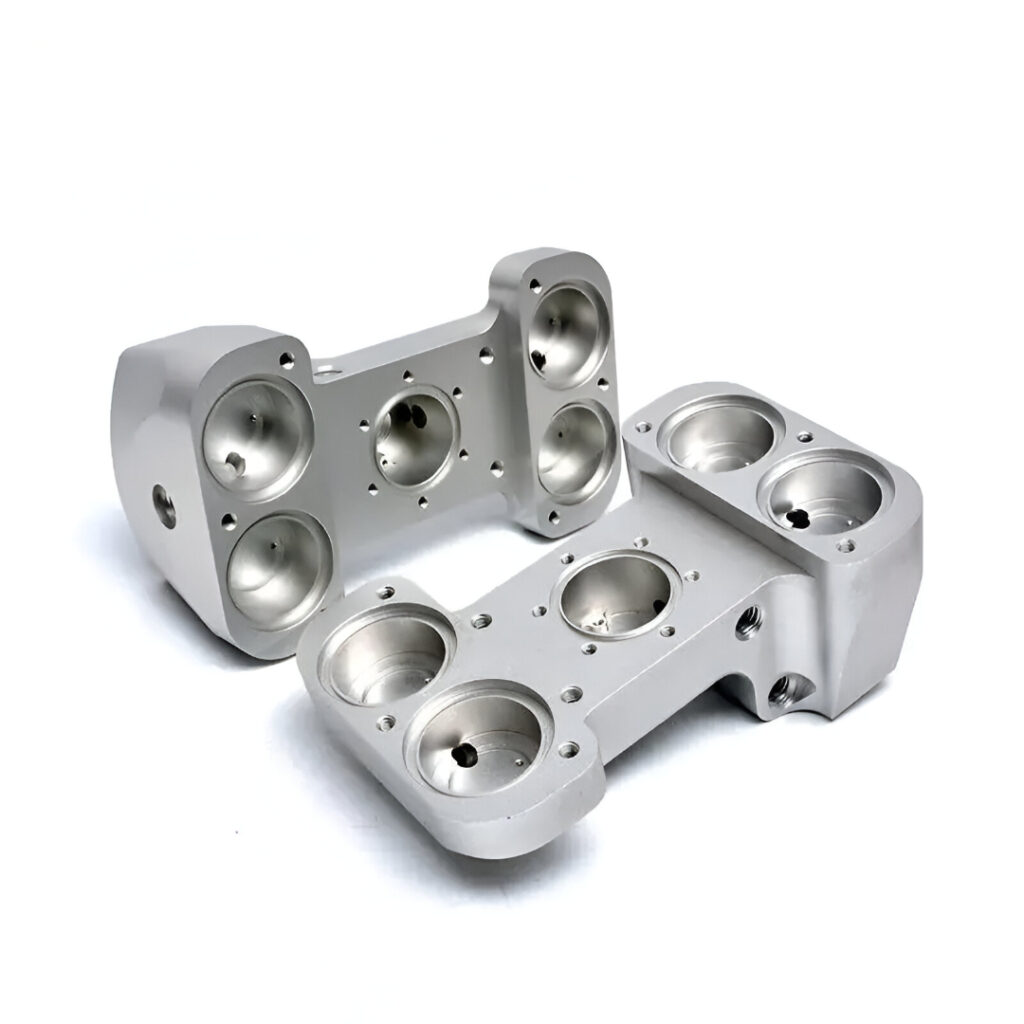
Every stage of production at Global Precision Pvt Ltd incorporates quality assurance –
- Only certified aluminum billets and bars are allowed to enter the shop floor thanks to incoming material inspection.
- Using SPC tools and real-time data capture, in-process monitoring can identify deviations before they become problems.
- Coordinate measuring machines (CMM), laser scanners, and optical comparators are used in the final inspection to confirm surface integrity and dimensional accuracy.
- Lean Six Sigma techniques are used in continuous improvement programs to cut waste and improve process stability.
Innovation is equally important. To push the limits of what aluminum components can accomplish, our R&D team is constantly investigating new alloys, surface treatments (such as plating and anodizing), and hybrid machining-finishing methods.
Overcoming Challenges in Aluminum Turning
Aluminum has many benefits, but it also has certain drawbacks.
- Chatter and vibration – Needs machine rigidity and optimal tooling.
- Built-Up Edge Formation – Requires the right cutting parameters and tool coatings.
- Thermal Expansion – To maintain tolerances, careful compensation in CNC programming is required.
- Chip Control – Workpiece and tooling damage is avoided by efficient chip evacuation systems.
Through meticulous process development, cutting-edge tooling partnerships, and ongoing technical team training, Global Precision Pvt Ltd tackles these issues.
Future Trends
Autonomous driving and electrification are changing the automotive landscape, bringing with them new demands –
- Lightweight Platforms – More aluminum will be used as weight reduction objectives are pursued.
- Combining sensors and actuators – Tiny, repurposed parts for steering and electric motors.
- Sustainability Certifications – OEMs will demand that suppliers show that they have reduced their carbon footprint by optimizing their processes and choosing materials.
Automotive manufacturers can maintain a competitive edge and stay ahead of these trends by collaborating with a forward-thinking component manufacturing company like Global Precision Pvt Ltd.
Conclusion
Aluminum Turned Components for Auto Industry are essential for reaching performance, efficiency, and sustainability goals in the cutthroat automotive market of today. Every component is made with accuracy, dependability, and creativity when you work with a respectable component manufacturing company. Global Precision Pvt Ltd offers turnkey solutions that advance your automotive projects by fusing state-of-the-art technology, extensive material knowledge, and customer-focused service.
Get in touch with our engineering team for a meeting and sample parts review to find out more about how Global Precision Pvt Ltd can improve your automotive component manufacturing. Allow us to assist you in promoting excellence and innovation in each vehicle you manufacture.